Seventy-two combat engineers with the 530th Engineer Company, 92nd Engineer Battalion, 3rd Heavy Brigade Combat Team pushed themselves for five days and four nights this week, vying to earn the title “Expert Sapper,” 92nd Engineer Battalion Rear Detachment Commander Capt. Dennis Louck said.
First Sgt. Richard Hundley, the unit’s command sergeant major-rear, said combat engineers — particularly those who’ve completed the month-long SAPPER course at Fort Leonard Wood, Mo. — build obstacles and construct things like bridges. They also breech obstacles and destroy bridges and other structures, he said.
In Iraq and Afghanistan, however, the primary mission of the 3rd Infantry Division’s combat engineers has been route clearance — finding and destroying improvised explosive devices, according to 530th Eng. Company Commander Capt. Chris Blackburn.
“SAPPERS clear the way,” Blackburn said. “But since we returned from downrange back in March, we’ve focused all our training on basic soldier skills and basic combat-engineer skills. They (went) through 16 events each day this week, from 7 (a.m.) to 11 (p.m.). Everyone goes through the training.”
Blackburn said the combination of testing and training was a validation of the previous months’ training.
He said some of the soldier skills that were tested included a combat lifesaver’s lane, an individual marksmanship live-fire; a physical-fitness training test that included push-ups, sit-ups and a 2.5-mile run; a 12-mile ruck march; and a dismounted land-navigation course that was 25 kilometers long.
Blackburn said the combat engineer/SAPPER skills tested included urban breeching, field-expedient demolition, knot-tying, making a poncho-raft, swimming, dismounted clearance of a footpath and identification of explosive hazards.
The explosive-hazard identification lane especially is important for combat engineers, he said, because when they come upon an IED, they have to know what kind of explosive is being used in order to know the best way to destroy it.
He added that in Iraq, most IEDs were made from military munitions, but in Afghanistan, most IEDs tend to be homemade explosives.
The field-expedient demolition task was at what is called the “grapeshot” lane, Blackburn said.
“What they’re making here is pretty much a field-expedient Claymore mine,” he said, noting the components the soldiers were packing in gallon-size cans. “Once the soldier lays the charge in position, he aims it just like he would a Claymore, then attaches a shock tube (detonator) to a det-cord loop.”
Spc. Garrett Carlson, a Houston native, took on the prone position to adjust the aim of his charge, then carefully attached the blasting cap through the detonating-cord loop protruding from the bottom of the can. The blasting cap already was attached to the end of the shock tube, a thin-diameter plastic tube filled with an explosive.
When all soldiers had laid in their charges and unrolled their lines, the safety noncommissioned officer gave the OK for the soldiers to fire their charges. One by one, each man shouted, “Fire in the hole, fire in the hole, fire in the hole.”
Following the third warning, a spark and a black cloud appeared among the silhouettes downrange, which immediately was followed by a blast.
At the light-breech lane, engineers hooked a det-cord loop over a large nail simulating a door knob then attached it to the shock tube. The soldiers crowded behind a ballistic blanket to fire the explosive, which blew a hole in the door where the door knob used to be.
“Unlike TNT or dynamite, C4 cuts through whatever we’re trying to breech,” Blackburn explained. “The explosive from TNT and dynamite tends to push more so than cut. That’s why we use C4 to cut through things like a steel I-beam on a bridge. Our engineers have to calculate how much C4 is needed to cut through a steel I-beam or a tree.”
Blackburn, who is a SAPPER and Ranger-qualified engineer officer, has completed one combat tour in Iraq and two tours in Afghanistan.
'Sappers' learn to blow things up
Combat engineers vie for expert status
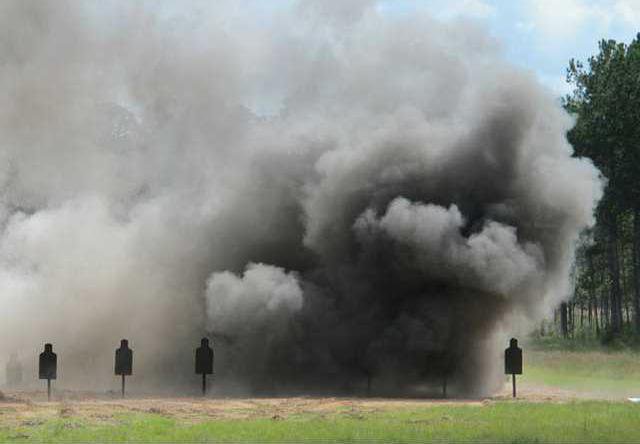
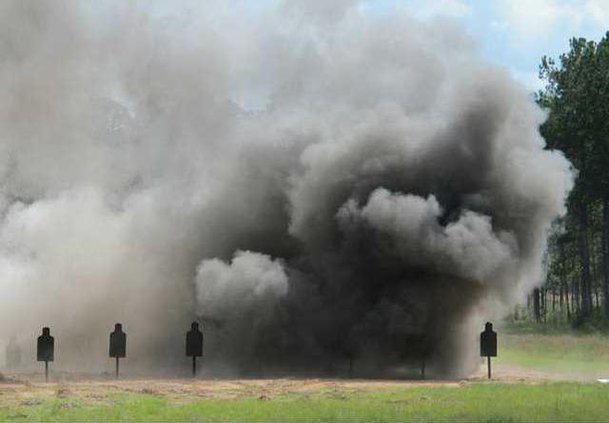
Sign up for our e-newsletters